How to conduct an Accident Investigation using the 5-Whys: A Case Study.
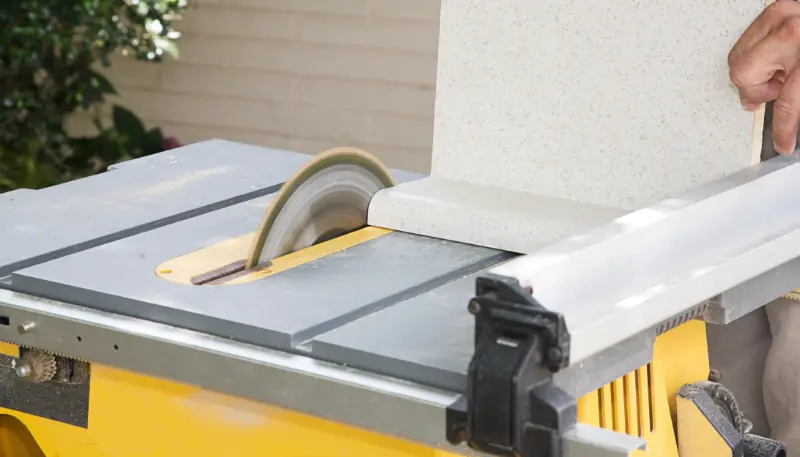
1. Introduction.
Knowing how to conduct an accident investigation using the 5 Whys method is fundamental knowledge that all health and safety officers should have.
All workplaces in Ireland must comply with the Safety, Health and Welfare at Work Act 2005. The purpose of this Act, along with the Safety, Health and Welfare at Work (General Application) Regulations 2007, is to prevent accidents in the workplace. However, accidents still happen because, unfortunately, people make mistakes and do things that they shouldn’t, or organisations act in a way that puts their employees in danger. When this happens, the company should conduct an accident investigation to find out the root cause of the accident, and if the company does not employ a person qualified to conduct the investigation, they should use an outside contractor that is suitably qualified.
This redacted case study is of an accident that actually happened and the subsequent investigation that followed it.
2. Workers Accident details
The accident occurred to the injured person (IP) at a kitchen manufacturing company that employed 25 people. The IP worked in the workshop with nine others. He was shaping a piece of hardwood on a professional table saw, as shown in the below image when he was distracted. He was distracted because part of the wood he was cutting broke in the saw and was ejected. When the break happened, he looked away from the saw toward the ejected piece, and his free hand came into contact with the exposed spinning saw blade.
3. The Sequence of events
The image below sets out the timeline between the task being started by the IP selecting the wood and having the accident. It was approximately 30 minutes, but as there was no CCTV, this is the recollection of the IP.
4. Immediate actions
After the accident, the IP summoned a colleague, who, after seeing the injury, called the workshop foreman. He, in turn, looked at the injury and summoned the owner of the business who was onsite. After seeing the injury’s apparent severity, the business owner then took the IP to the A&E, which was 20 minutes away, where he was immediately attended to.
No work resumed on the day of the accident. The workshop gradually resumed production over the following five working days.
5. Injuries received
The local A&E dressed the IP’s wounds and then he was taken by ambulance to a specialised hospital for plastic surgery. He was operated on the same day where they amputated the top of his fourth finger. They fused the knuckles on his second and third fingers as they had been cut through. His index finger had severe and deep lacerations. He also had extensive ligament, tendon and nerve damage to all fingers. He had more corrective plastic surgery two days after the first operation and was discharged a further two days later. He was given a prescription for morphine for the pain on discharge.
6. Findings
A comprehensive survey, initially of the workshop and subsequently of the available documentation was carried out. The finding of this is set out below.
6.1 Information gathered
The workshop was new, the company had recently moved into it and was fitted out with new state of the art machinery and equipment. The correct machine for the task the IP was performing was in use, so he chose an alternative which was a large table saw. The table saw was not suitable for the task but was used to complete the task in order to get the job done.
There was no booking system to allocate time to use each machine, it was done on an Adhoc first come first serve basis.
The IP did not start another task and wait for the correct machine to become available; instead, he used the table saw. The fence on the table saw had been calibrated incorrectly, it was not set parallel to the saw disc, so the workpiece was being pinched between the fence (guide) and the saw blade as it travelled through the saw. The guard designed to cover the exposed saw blade was higher than it should have been, exposing more of the blade than necessary. The saw blade was also sitting too high in the machine, again exposing more of the blade than was necessary, thus exposing the operator to more risk.
6.2 Existing risk assessments & procedures
There were no risk assessments completed for the new machinery. This was because there was no member of staff qualified or competent to perform a risk assessment on the new machinery and no outside contractor was or had been engaged to complete one. There was no safety statement completed for the business. There was no evidence of any Health and Safety training being completed at the company either for any of the machinery or for any members of staff.
When looking for Standard Operating Procedures (SOP’s) or Safe Systems of Work (SSoW), again there were none present.
6.3 Interviews
Interviews were carried on with the injured person, the company owner and two of the injured persons work colleagues. A brief synopsis of the interviews is below and a copy of the originals have been added to the appendices.
Injured person
The injured person is now aware that the saw that he was using was not calibrated correctly. He allocates the blame to the machinery supplier that installed the machine.
Company owner
The company owners opinion is that the machine was not calibrated correctly when it was installed. He also allocates the blame to the machinery supplier that installed the machine.
Colleague 1
The injured persons coleague was the first on scene. He heard the saw cutting through the the hand and turned to see the injured person holding his hand close to his chest. He also saw the blood on the saw and on his chest and the look on his face. He commented that he will never forget that scene. He said that in his opinion the injured person had selected the wrong machine for the job, but realised the IP did this because the correct machine was already in use by another operator.
6.4 Root causes
The Five whys technique was used as a root cause analysis system to discover the reasons for the accident happening. This is shown in Figure 5.1, which begins to show the causes for the accident happening.
The analysis carries on as can be seen in the below graphic which reveals the root causes of the accident.
6.5 Training
When looking for documentation regarding training records for the new machines they were not present. No training was provided to the staff by the machinery company: the only training given was cursory training given to the owner of the company along with the instruction manuals by the installing company. The owner passed this information on to the employees along with the manuals which were found in their wrappers in the drawer next to the machines. So, the staff were never trained in the correct use of the new machinery.
6.6 Maintenance, inspections, audits
The workshop along with all machinery was new and set up 6 weeks before the accident. For this reason, there had been no requirement for any maintenance for the machines or audits for their efficiency or reliability.
7. Accident causation
From the root cause analysis, the causes for the accident have been identified. These causes have been set out below.
7.1 Immediate causes
- The workshop was busy but the task had to be completed.
- The saw was not correctly calibrated so the fence was not running parallel to the saw blade.
- The operator was not trained on the machine so was not fully competent.
7.2 Underlying causes
- Time pressures to complete tasks
- No task project management
- No Safe Systems of work for each machine
- Machines not commissioned correctly or checked to be in compliance
7.3 Root causes
- Owner failed to recognise the need for training and staff competence
- Owner did not perform any risk assessments
- Owner lacks competence so could not address any of his responsibilities for H&S
- There was a lack of supervision and no organisational management
8. Conclusions
It is the opinion of the injured party, his colleague and the business owner that the cause of the accident was the incorrect calibration of the table saw when it was installed. This is the reason why their witness statements and their conversations are short because they believe the reason for the accident is the immediate cause.
The facts say that there has been no training in health & safety in any aspect within the company and there have been no risk assessments completed. The individual qualifications of all members have staff were never requested or checked but were taken at face value.
The root causes of the accident fall with the business owner as, in this case, he is the responsible person. However, blaming that one person for an accident that was contributed to by more than one person is not productive and would not prevent the accident from happening again.
9. Recommendations
The Health and Safety in the company has been reviewed and to bring the company into compliance the following recommendations should be completed within 1 month of the date of the report.
The table below shows the Recommendations made to improve Health & Safety
Prior to publication, this report has been reviewed by my senior colleague who found it to be a fair reflection of the accident, its causation and the recommendations.
The owner of the company has also read it and fully supports the findings and its recommendations. He has also given assurance that the company will be in compliance with the specified timeframe.
9.1 Witness statements
Witness Statement from the Injured Party
Privileges and Confidential – this presentation is prepared for the purposes of consideration by ABC Co Ltd and its Legal Advisors in contemplation of legal proceedings taken against ABS Co Ltd
Name Injured Party (Injured Person) Job Title Cabinet Maker
Address. County Kildare
Incident; Accident at the workplace causing hand injury
Statement.
Hi IP, can you explain to me what happened leading up to the accident.
It was a normal day. I had a meeting with a customer I was making a kitchen for in the morning, and we agreed on the design. I then took a break and when returning I began the work. I selected a piece of wood that I could machine down to 10mm square and then shape into the required design. The machine to do this is called a planer/thicknesser but that was already in use, so I decided to use another machine to do the job with. The machine I chose was the table saw. This is usually used for bigger pieces of timber, but it would do the job. I set the fence of the saw to the required size and started to feed the wood to the saw and began making the cut. It was going smoothly but then it seemed to get more difficult to push the wood through the saw. The wood then seemed to break in the saw and flew across the room, I followed it with my eyes and as I turned my body right hand hit the saw blade. I immediately knew what happened and clasped my injured hand to my body and called for help.
What do you think happened to cause the accident?
I think that the fence on the saw was not running straight with the saw blade and as I pushed the wood through the saw the gap between the blade and fence got smaller and squashed the wood until it broke and flew out of the machine.
Why do you think that happened?
The fence on the machine should have been straight with the blade especially as the machines are new, but it wasn’t on this machine, and I don’t know why. I don’t think the machine was set up wrong when it was fitted.
What would you do to prevent this from happening again?
I would get the firm back that fitted it and tell them to fix the machine so that it works properly
Is there anything else you can tell me about your accident?
No not really. I just wish I had been trained to use the machine, if I had been I would still be working there today
I have read this statement and confirm the contents are true and accurate to the best of my knowledge
Signature if Person Making Statement ____________________ Print Name Injured Party
Signature of Investigation Team member __________________Print Name Mark Williams
Dated 14-12-2021 Page Number 1 of 1 page
Witness Statement from Witness
Privileges and Confidential – this presentation is prepared for the purposes of consideration by ABC Co Ltd and its Legal Advisors in contemplation of legal proceedings taken against ABS Co Ltd
Name Witness (Work colleague) Job Title Cabinet maker
Address. County Kildare
Incident; Accident at the workplace causing hand injury
Statement.
Hi Eamon, can you explain to me what happened leading up to the accident.
I didn’t actually see the accident, but I did hear it. I heard the saw cutting through The IP’s fingers and hand and turned around as I was only a few feet away to see him holding his hand to his chest. I could see blood on the machine and blood all over his hands and chest and the look on his face. I don’t think I will ever be able to forget what I saw that day.
Ok, what do you think happened to cause the accident?
The IP said he was using the table saw to cut down a piece of wood to 10mm square, I thought this was strange as he should have used the planer/thicknesser. He told me Mick was using that though, so he decided to use the table saw instead. I wouldn’t have used that as it’s designed for bigger wood, not the intricate work that he was doing as the blade is exposed. On the planer/thicknesser, you can’t touch the cutters as they’re hidden which make it safer. I guess he just wanted to get the job done for the customer.
Why do you think that happened?
As I said, I think he used the machine which wasn’t the best fit for the job.
What would you do to prevent this from happening again?
Maybe have signs on the machine saying what you can and can’t do on each machine? Or a training course to tell us how to use them properly, we need something anyway or it will happen again.
Is there anything else you can tell me about the accident?
No, not really. I feel sorry for The IP and the pain he’s going through, looking at it now its an easy accident to avoid but that’s an easy thing to say after the fact
I have read this statement and confirm the contents are true and accurate to the best of my knowledge
Signature if Person Making Statement ____________________ Print Name Witness
Signature of Investigation Team member __________________Print Name Mark Williams
Dated 14-12-2021 Page Number 1 of 1 page
Witness Statement from Director
Privileges and Confidential – this presentation is prepared for the purposes of consideration by ABC Co Ltd and its Legal Advisors in contemplation of legal proceedings taken against ABS Co Ltd
Name Director (Company Owner) Job Title Owner
Address. County Kildare
Incident; Accident at the workplace causing hand injury
Statement.
Hi Tony, can you explain to me what happened leading up to the accident.
I didn’t actually see the accident as I wasn’t in the workshop at the time.
Ok, what do you think happened to cause the accident?
My experience tells me that the fence was not correctly calibrated to the saw and because of this the wood grabbed in the saw and spat it out. This wouldn’t have been noticed so much with bigger pieces of wood, but The IP was working on a small piece that is weaker which is why it broke.
Why do you think that happened?
When the machines were installed, they were shown to me that they were all working, and I was given the machine’s instructions which were books of information on how to set up the machines. I had assumed that the machines had been calibrated by the installer, but they had not done this. This is why the accident happened.
What would you do to prevent this from happening again?
The company that installed the machine is coming back now to check all of the machines. This will stop the accident from happening again.
Is there anything else you can tell me about the accident?
I’m just sorry that it happened, and I wish it hadn’t happened. The machine company assures me that the machine will be checked and calibrated if necessary before it is used again.
I have read this statement and confirm the contents are true and accurate to the best of my knowledge
Signature if Person Making Statement ____________________ Print Name Director
Signature of Investigation Team member __________________Print Name Mark Williams
Dated 14-12-2021 Page Number 1 of 1 page
© SafetyTraining.ie 2024